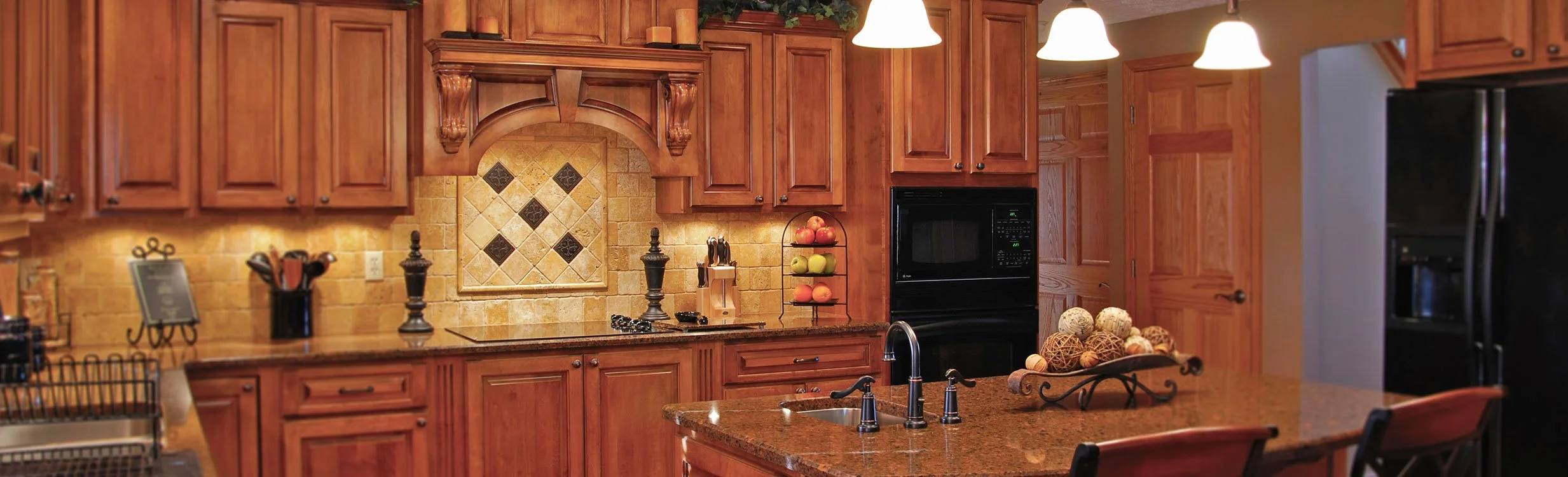
CASE STUDY 3
UNIQUE STATISTICS
40
LOADS PER WEEK
200
TOTAL STOPS
15
DROPPED TRAILERS
Challenge
Our customer’s requirements dictated multi-state, multiple drop loads, with extra stops often being added at the last minute to many of the loads going out on a given day. They were experiencing seasonal tightening in their market, and were forced to use unknown carriers at inflated pricing, which many times yielded poor results. With no ability to implement a real dock schedule, they had to live load trailers as carriers arrived for pick-up. This way of working put tremendous pressure on their dock personnel, who had to pull individual product lines from various locations in their warehouse and stage each load correctly for the various drops. It was expensive, time consuming, prone to errors, and stressful. With the complexity of their supply chain, they were finding it very difficult to find reliable capacity that didn’t blow up their transportation budget.
Solution
Tumalo Creek has been Quality One Woodworking’s primary logistics provider for over 8 years. We started out by designing and implementing a combination drop trailer/live load program that significantly reduced their supply chain expense and streamlined their loading operations. Being able to pre-load a dropped trailer allows Quality to more carefully manage their multi-drop loads, and significantly reduces the stress of their dock personnel. We have greatly reduced their capacity issues, and Quality can count on our load planners and customer service representatives to keep them in the loop and communicate with them, not only when things are running smoothly, but when things tighten up during difficult seasonal periods. Quality One has come to rely on Tumalo Creek as a true partner in getting their products to their customers on time and intact.
Case Studies
Banks Outdoors
Intera Materials
TVS /Mountain Maid
Quality One Woodworking